An air intake manifold is an integrated assembly that sits atop the engine, consisting of a series of tubes which distribute fresh outside air to each and every cylinder. On V-shaped engine blocks, an intake manifold typically sits between the two cylinder banks while inline engines may feature a manifold to the side of the cylinder head. Intake manifolds serve as a mounting point for carburetors, throttle body assemblies, fuel injectors, thermostats, and more depending on vehicle manufacturer engineering preferences. Intake manifolds also serve to route coolant through dedicated channels in order to remove heat from the engine. Needless to say, intake manifold assemblies are under constant stress from engine vacuum pressure as well as direct heat from coolant, cylinder combustion gasses, and the adjacent cylinder heads they are mounted to.

Intake manifolds for inline engines are often mounted on the side of the engine block, as seen in this diagram.
Until the 1990s, most intake manifold assemblies were made from cast iron when lower cost was a predominant factor, or from aluminum when lighter weight was judged more important for performance reasons. Because newly-developed intake manifolds molded from plastic offered both very low weight and lower cost, they began to gain popularity during that decade as original equipment once automakers figured out how to cast them in a form that was durable enough to survive preliminary testing. In this article, we’ll discuss flaws of early plastic intake manifolds that gave them an unfair reputation, and we’ll discuss how those issues have been addressed in quality replacement ones that can be purchased today.
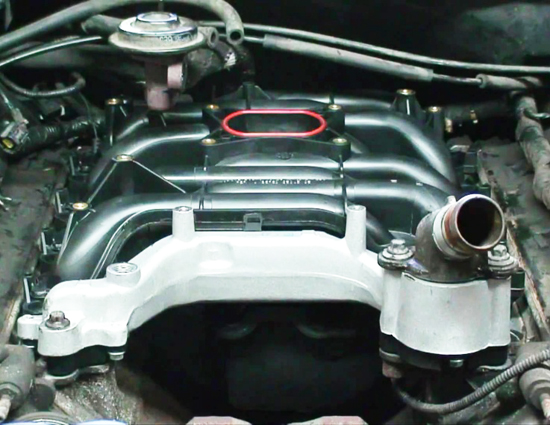
Intake manifolds on V-shaped engines are typically mounted on top of the engine between both cylinder banks, as seen on this Ford 4.6-liter V8.
PLASTIC INTAKE MANIFOLDS HAVE GOTTEN A BAD RAP FROM FLAWED EARLY DESIGNS

Early plastic intake manifolds such as this one for a 1990s inline 4-cylinder were often under-engineered and prone to failure because they could not handle under hood heat and pressure. External cracks, warping, and internal decay from dirty coolant were common results.
What was not originally factored in by car company engineers was extended real-world use. Early original equipment designs were biased toward keeping down overall manufacturing costs, so early intake manifolds were not overbuilt. Vehicle manufacturers may not have intentionally cut corners, but little was known at that point how well plastic intake manifolds would really hold up over time or what might cause them to fail. The first designs ended up being flawed, and original plastic intake manifolds used on 1990s General Motors 3.8-liter V6s, Ford 4.6-liter V8s, and Chrysler 4.7-liter V8s are among the more notorious examples of designs prone to early failure.

Plastic naturally dries out and becomes brittle with the passage of time. Compounds used in early intake manifolds like this one were often cast too thin, and were subject to cracks and breakage due to inadequate reinforcement around external fittings.
Dissimilar materials such as plastic, aluminum, and iron all have different expansion and contraction rates as they change temperature, so gaskets that provide a seal between an intake manifold and a metal cylinder head must be flexible and durable enough to withstand serious pulling and twisting forces. Early ones were not, and leaks resulted along with warpage under intense heat that eventually led to cracks.
Coolant that’s too old and deteriorated can be corrosive to plastic, and walls of the tubes carrying anti-freeze inside the manifold tend to be eaten away gradually by this. Early designs did not account for this, eventually leaking coolant directly into the cylinders when tube walls gave out. While a little coolant causes rough running, too much coolant can cause an engine to seize up completely because water cannot be compressed.
Like any oil-based product, plastic can become dried out and brittle with the passage of time – especially when subjected to intense heat. Without proper reinforcement, fittings on the outside of early manifolds for exhaust gas recirculation (EGR) valves, heater hoses, thermostats, temperature sensors, and other items were prone to cracking off completely. Ford even mounted alternator supports directly to their 1996-2001 plastic manifolds, and that extra weight eventually led to large scale cracks and failure.
IMPROVED PLASTIC COMPOSITES AND DESIGNS HAVE MADE TODAY’S INTAKE MANIFOLDS FAR SUPERIOR
In recent years, more and more automakers have switched to plastic intake manifolds. After decades of testing and studying common failure points, optimum blends of plastic with 35% fiberglass or related glass elements have been perfected to enhance both strength and elasticity. Today’s plastic intake manifolds are more than just mere plastic. Greater strength from engineered compounds resists cracks under pressure where it’s most needed, and greater elasticity yields the ability to stretch and snap back – preventing permanent warpage which causes leaks. Failure rates of quality plastic intake manifolds manufactured since the beginning of this decade have dropped significantly, and we feel high reliability over long-term use makes them a smart purchase.
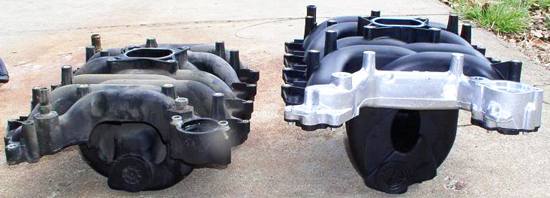
Shown from left to right in this picture are an original factory Ford 4.6-liter plastic intake manifold prone to failure, and an improved aftermarket version with aluminum reinforcements, better seals, and heavier-duty construction with improved plastic composites.

In this overhead view of an original factory Ford 4.6-liter plastic intake manifold (left) and an improved replacement (right), it’s easy to see how the OEM one lacks improvements such as fore-aft structural reinforcements, aluminum structural support in critical areas, better silicone seals, and strengthening around fitment areas. Look for as many of these features as possible when purchasing a replacement plastic intake manifold.
Thicker construction in critical areas prevents erosion from dirty coolant, and the addition of aluminum reinforcements provides increased load-bearing capacity for external fittings and components. Plastic compounds dissipate heat better than metal, so air flowing through intake tubes remains cooler to aid combustion. Sound-deadening acoustic qualities of newer compounds have been improved, eliminating raucous and unwanted engine noise like the best heavy metal manifolds. Silicone-based gaskets allow better flex between dissimilar materials, and they help eliminate corrosion and vibrations. If you’re considering purchasing a plastic intake manifold, look for one with these improvements.